Project of the Year Feature: Residential
January 23, 2025
BURR RIDGE – CISCO’s 6th 2024 Project of the Year Feature is the top choice of Residential, which is the Solverre. General contractor was Gilbane; the client was Willow Bridge Company (previously Lincoln Property Company).
When considering submissions, judging criteria is based on: quality of construction, design, impact on the community and safety record.
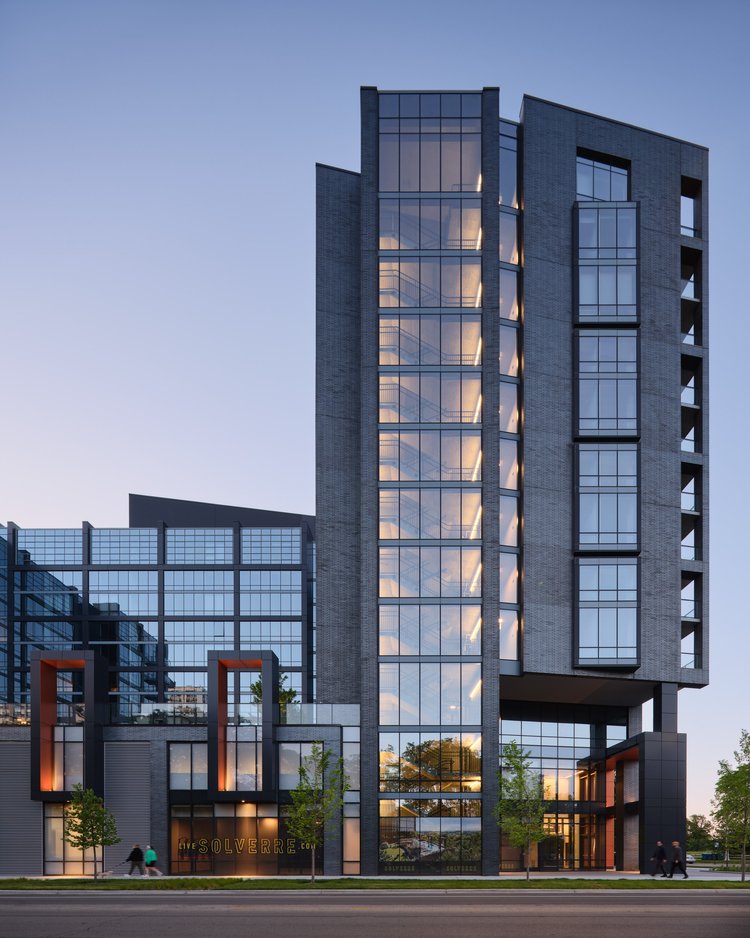
Solverre at 4600 N. Marine Drive, developed by Willow Bridge Property Company, is a luxury Class A rental apartment community. This new 12-story residential development is situated on a one-acre plot in the vibrant Uptown neighborhood in Chicago, Illinois and comprises approximately 303 rental units with an above-ground parking facility.
The 12-story building, constructed with a blend of innovative techniques and traditional craftsmanship, offers a variety of living spaces from studios to two-bedroom apartments. Residents enjoy a best-in-class amenity package, including a pool deck, fireplaces, grills, bike storage, a dog room, a business center, club rooms, a yoga studio, and a fitness room.
The project achieved significant community engagement with 21.56 percent participation from minority-/women- business enterprises (M/WBE) and 33 percent of construction jobs were filled by local residents, highlighting Gilbane’s commitment to inclusivity and economic empowerment.
The building’s contemporary design harmonizes with the surrounding urban landscape, providing unobstructed views of Lake Michigan and the Chicago skyline. Solverre is a testament to urban vitality and is an example of how architecture and construction transform a space, create a community, and enhance the quality of life for its residents.
Solverre’s sleek lines and contemporary façade harmonize with the surrounding urban landscape, creating an architectural masterpiece that complements the Chicago skyline. The building includes several distinctive architectural features and is the first precast building in North America to adhere to the Precast/Prestressed Concrete Institute’s stringent construction tolerances. Erected by a PCI-certified erector, Solverre is classified as an AB project, indicating its complexity in precast design. The seamless integration of precast brick panels with field brick and custom window wall detailing creates a visually stunning façade.
Strategically positioned egress stairs and an elevator lobby along the exterior create natural light and promote use and passive surveillance. Additional features like floor-to-ceiling windows, etched glass, and dark gray brick and metal accents add a contemporary touch to the building’s exterior. The central sundeck, nestled within the U-shaped structure, offers residents impressive views and abundant natural light.
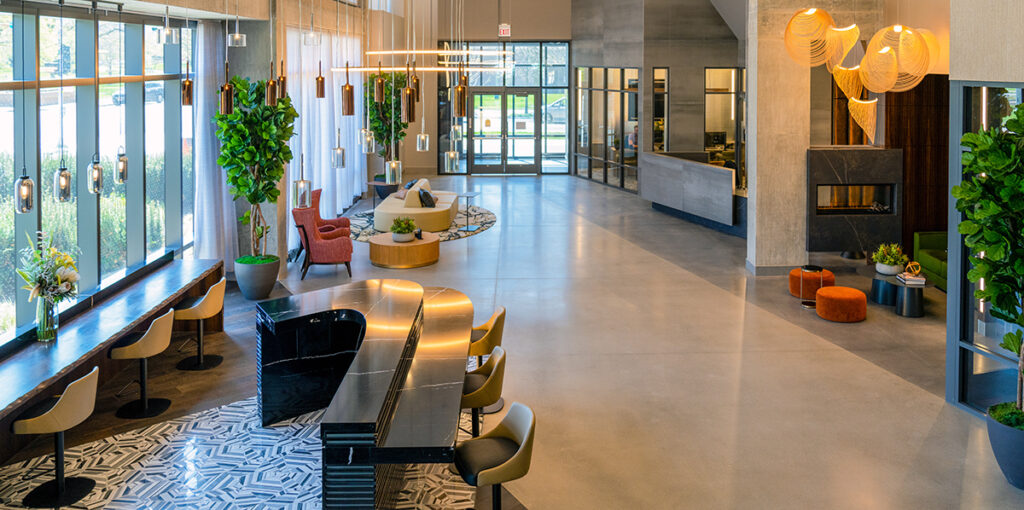
The construction team employed a series of innovative strategies and fostered early partnerships with key contractors, resulting in substantial cost savings of $8 million. Initially envisioned as a framed structure, Solverre underwent a comprehensive structural evaluation to explore cost-effective solutions. The team thoroughly evaluated the most economical structure, comparing the steel truss panel system with concrete.
Prior to the completion of the design, early partnerships were forged with the concrete, architectural precast, window wall, and MEP/FP trade contractors. These early collaborations drove the most effective and economical outcomes for the installation and detailing of the building’s skin and critical MEP systems. This ensured that all elements were designed and installed efficiently, cost- effectively, and to the highest quality standards. Through these measures, the Gilbane team demonstrated their commitment to excellence and innovation in construction.
Located in a vibrant neighborhood, Solverre prioritizes public space and the resident/pedestrian experience. High resident satisfaction underscores the project’s positive impact on the Uptown community and Chicago’s architectural landscape. The design goals were met, end users are satisfied, and the quality of craftsmanship exemplifies excellence.
The design process began in December 2019 and encountered an unforeseen obstacle — the Covid-19 pandemic. The design team quickly adjusted workflows, collaborating closely with the city’s Department of Planning and Development and the neighborhood’s alderman to ensure the project’s progression while prioritizing the health and safety of the entire team.
However, the pandemic triggered supply chain disruptions, particularly impacting the availability of insulation and waterproofing materials. The design and construction team promptly evaluated all exterior building conditions and adjusted construction details based on material availability and constructability. This proactive approach ensured the project remained on schedule while maintaining stringent quality and safety standards.

As the project progressed, the exterior enclosure materials and systems underwent significant modifications during the design development phase. Gilbane and Valerio Dewalt Train collaborated with the manufacturer to transform the original exterior grid into an elegant window wall. This transformation facilitated unique design solutions across the building envelope at various intersections, enhancing both aesthetics and functionality while also reducing costs.
Solverre, located adjacent to a highly active hospital, required meticulous construction site logistics. The construction team aligned material deliveries with the hospital’s operational requirements, ensuring zero disruption to the emergency department driveway and surrounding traffic routes. Hardscape protection measures were implemented to safeguard city streets, cyclists, and pedestrians from construction-related activities. The team also navigated an intricate urban infrastructure, a 130-foot water tunnel beneath the site that required close coordination with the city’s water department.
The construction of Solverre was a complex task that required precision, resilience, and teamwork. Despite challenges such as supply chain disruptions and intricate urban infrastructure, the team successfully completed the construction project on schedule and within budget. This accomplishment was achieved through careful planning, efficient execution, and collaborative problem-solving.
Solverre stands as a symbol of successful design and construction under challenging circumstances. The building is not just a structure, it’s a testament to the team’s ability to adapt and innovate in the face of adversity.
Solverre is a modern interpretation of the Uptown neighborhood’s historic brick vernacular. The building’s façade, a blend of dark brick cladding and expansive glass, harmonizes with its surroundings, creating a welcoming and pedestrian-friendly character. Beyond aesthetics, Solverre addresses a critical need in an area long challenged by housing shortages. Eight affordable housing units within the building underscored Willow Bridge Property Company’s commitment to community welfare. They also contributed over $3 million that directly supported a new 28-unit project led by Sarah’s Circle, a local organization dedicated to empowering women experiencing homelessness.
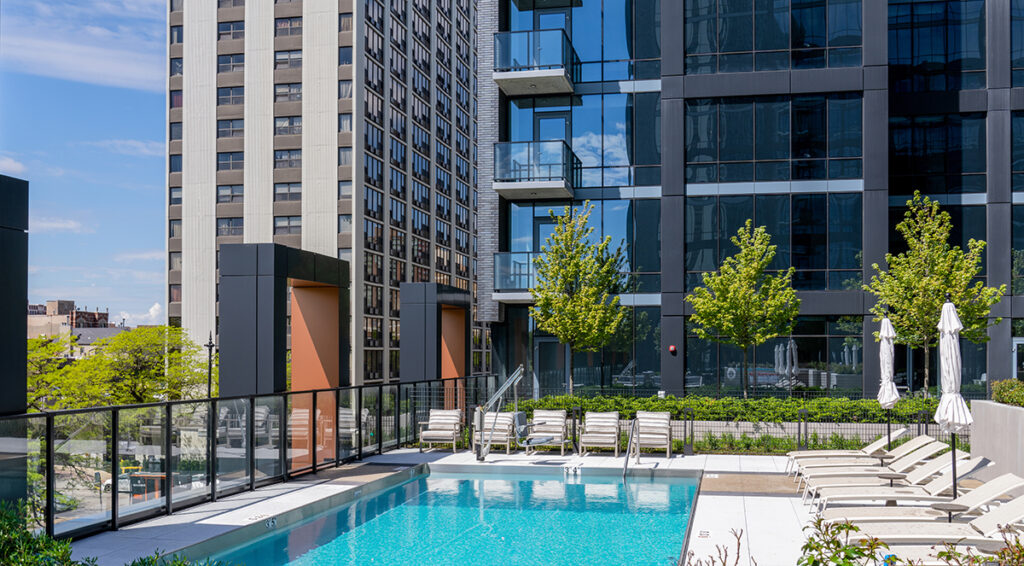
The project achieved 21.56 percent M/WBE participation, fostering inclusivity and economic empowerment. Furthermore, 33 percent of construction jobs were filled by local residents, reinforcing Gilbane’s commitment to the community’s workforce. Through these efforts, the project not only met its goals but also contributed to the fabric of community inclusion and diversity.
Aligned with Chicago’s Sustainable Development policy, Solverre champions energy and water efficiencies. The building features a green roof covering 50 percent of the surface area, achieving 20 percent energy savings over ASHRAE standards. Ample bicycle storage and EV charging stations are also thoughtfully provided. The first two floors also feature fritted glass that safeguards migrating bird populations, demonstrating environmental stewardship.
Gilbane leveraged cutting-edge 4D modeling by integrating the building’s design and construction models into our scheduling process. This approach allowed us to establish 4D model standards for virtual mock-ups and prefabricated construction zones while identifying any missed scope items for 303 residential units. Using these mockups, our team fine-tuned the millwork installation sequence and addressed vanity installation issues in each unit before construction began. By catching these issues early, we prevented significant rework and potential delays in the project schedule, ensuring all bathrooms were seamlessly constructed across all 12 floors. Utilizing this innovative and best-in-class tool enhanced team engagement and communication.
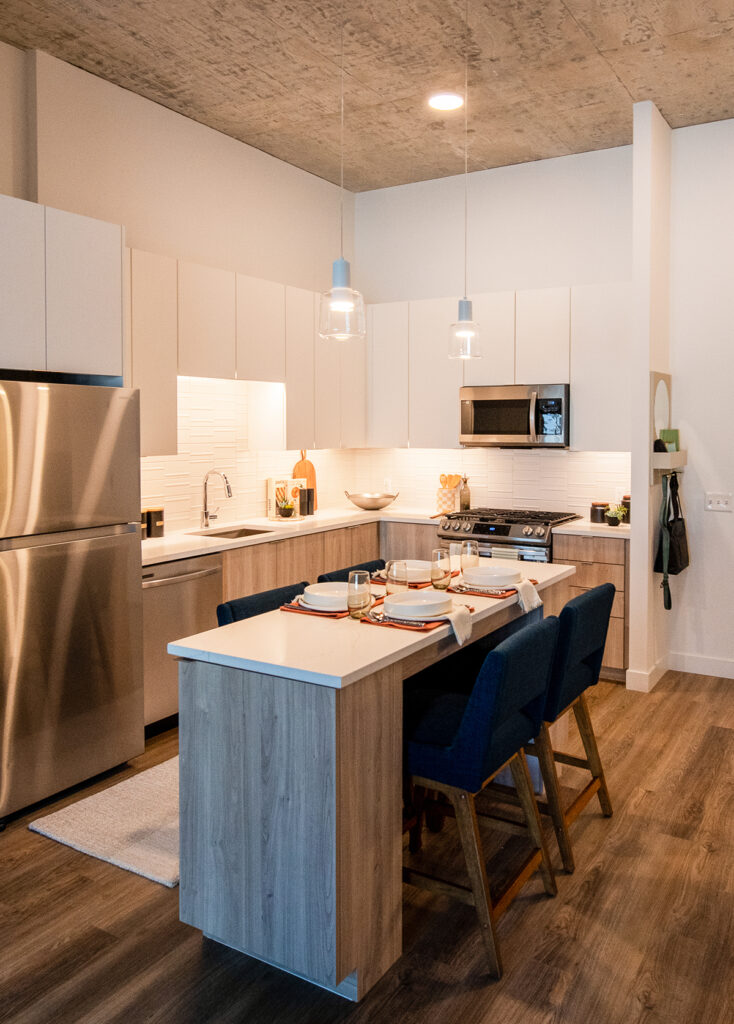
An unwavering commitment to safety lies at the heart of the Solverre. Rather than treating safety as a mere checklist, Gilbane’s project team recognized safety as a cultural necessity, a shared responsibility woven into every construction aspect of the project’s lifecycle.
The team implemented a multifaceted approach, starting with daily shift-start meetings. These meetings ensured that all trade contractors were brief on the day’s tasks and safety protocols. Pre-planning these meetings allowed for proactive hazard identification and risk mitigation, emphasizing the importance of preparation. Additionally, weekly foreman meetings facilitated communication and coordination among team leaders, reinforced safety practices, and addressed any potential concerns promptly.
Intensive training was a cornerstone, especially for high- risk activities such as working at heights, operating heavy machinery, and handling hazardous materials. Regular safety stand-downs empowered workers to actively monitor and correct unsafe behaviors. Mandatory scaffold erection and fall protection training was provided for all workers involved in elevated work, while emphasis was placed on proper shoring techniques and soil analysis during excavation work. By tailoring training to specific tasks, the workforce gained a comprehensive understanding of the risks associated with their work and learned effective mitigation strategies.
The project team conducted thorough investigations following any near misses, learning from each event to prevent recurrence. Our team did not just react to safety concerns; they proactively fostered a strong safety culture, focusing on continuous improvement to set a new standard for future industry projects. The project team exemplified safety excellence through a comprehensive approach.
› OSHA Recordable Incident Rate: 0.63
› Lost Time Accident Rate: 1.25
› Total Worker Hours on Job: 320,000
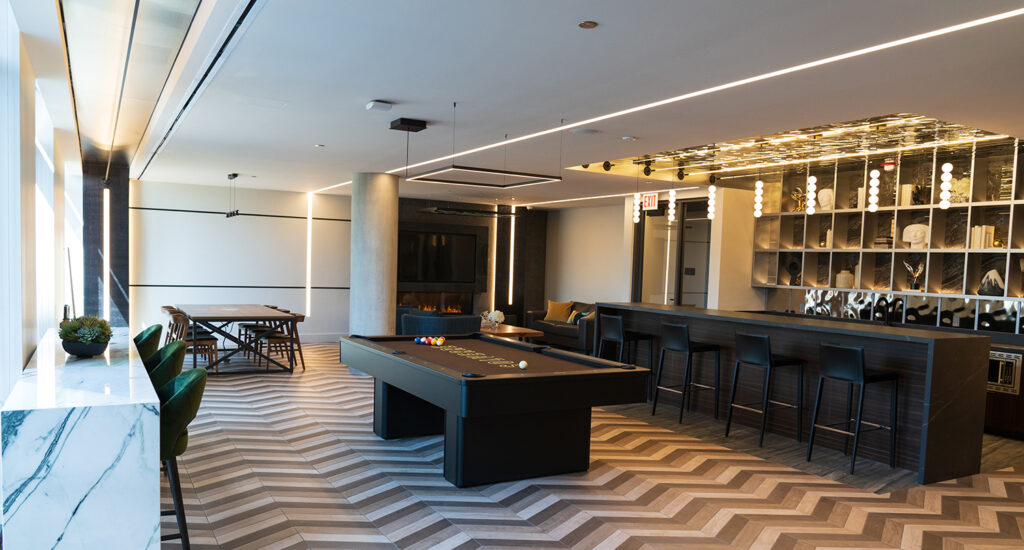
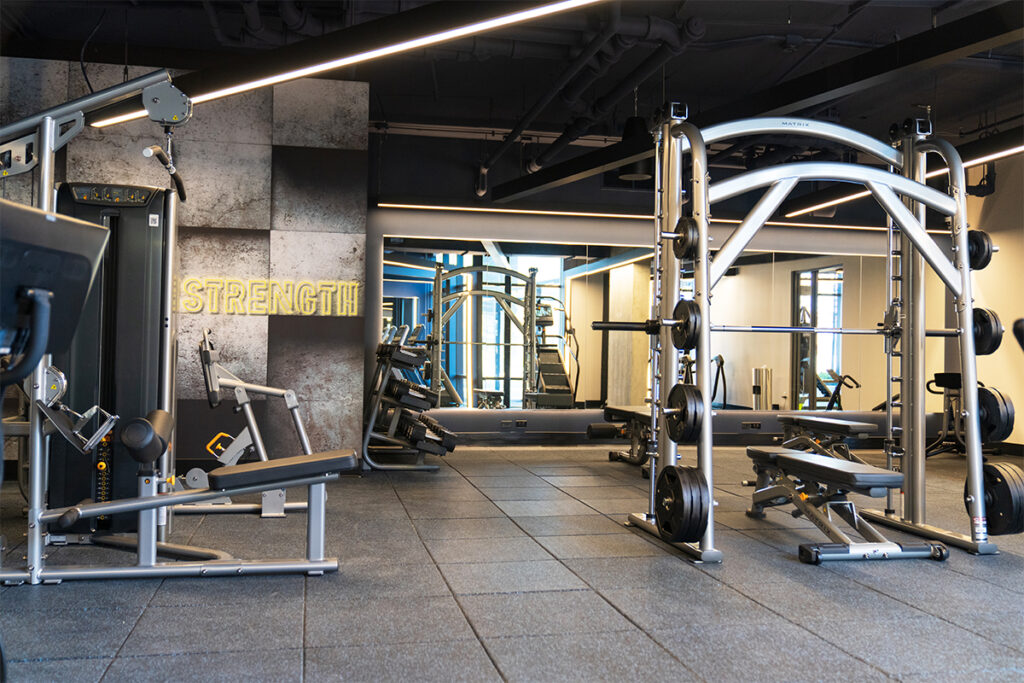